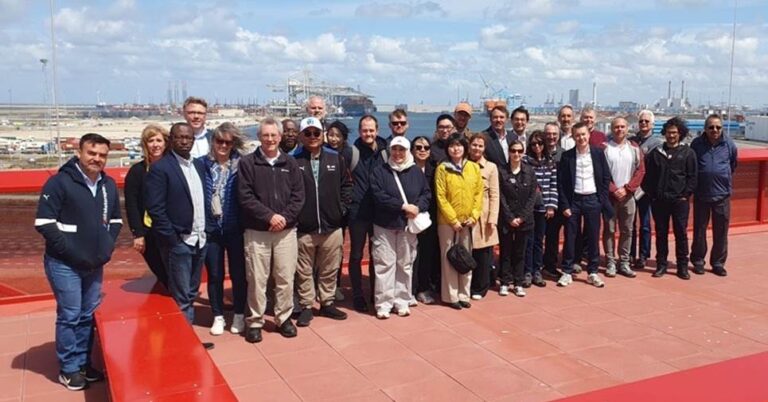
Final meeting CO₂stCAP Project
10 July 2019
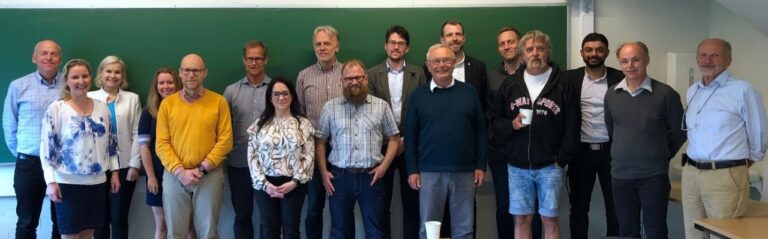
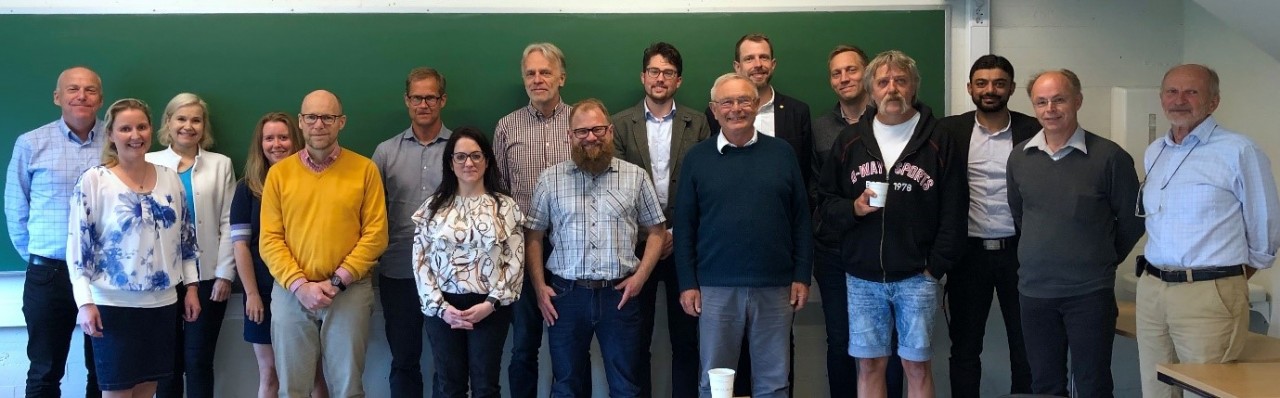
On the 13th June, I was delighted to attend the final meeting of the CO2stCAP project. This project is a Norwegian-Swedish initiative focused on cutting down CO2 capture costs in the industrial sector by implementing partial CO2 capture arrangements(see a previous meeting in https://ieaghg.org/ccs-resources/blog/co2stcap-partial-capture-on-industrial-sources). As we have discussed in our recent technical review (see 2018/TR03 Cost of CO2 capture in the industrial sector: cement and iron and steel industries), there is a significant opportunity on the industrial sector to optimize the heat/steam/energy (and in some cases materials) integration between the CO2 capture unit and the production facility based on the facility and regional context. Moreover, CO2 emissions in the industrial sector can be divided into process emissions (from the production process) and energy emissions (direct or indirect emissions from fuel combustion). In some industries, the process emissions are the most significant contribution to the total CO2 emissions, and CO2 capture is the only mature technology to reduce those at high extent.
The CO2stCAP project has investigated partial CO2 capture for the cement, silicon, pulp&paper and steel sectors, taking also into account the use of biomass and hydrogen as complementary decarbonising strategies, but also considering waste heat recovery and district heating arrangements for an optimum integration within the Scandinavian framework.
In this last phase of the project, the partners have delivered a more detailed assessment on CO2 capture costs, identified the optimum configurations, selected the most convenient CO2 stacks in each industry, and proposed the next steps to decarbonise the industrial sector in Scandinavian countries. Moreover, as this project is involving research organisations, academia, and industrial partners, it has been an optimum collaboration to integrate and understand new solutions for “real production facilities”.
As highlight of this project, the cost estimations included an on-site tool developed in SINTEF (before Tel-Tek University) to calculate the equipment costs. As examples, the preliminary increase on the product cost in the pulp&paper industry is 2-13%, and 4-17% in the steel, depending on the configuration and integration. Moreover, as we have discussed in parallel initiatives, the cost of the final product could potentially increase by just 1-4% (depending on the industry, final product and CO2 capture system). In this context, CO2 capture is a significant tool to decarbonise CO2 emissions (and more significantly process emissions) in the industrial sector due to the easy integration (of some technologies), maturity (of specific systems), and potential CO2 reduction.
For more information, you can see the IEAGHG webinar on the CO₂stCAP project held on the 25th June (https://www.youtube.com/watch?v=9tLLGKmMT9Y), which included presentations from Ragnhild Skagestad (SINTEF Industry), Max Bierman (Chalmers University), Anette Mathisen (SINTEF Industry), and Jens Wolf (RISE Bioeconomy). The speakers presented specific results on each industry and the attendees had the opportunity to ask additional details about the project and calculations.
As conclusion, it has been great to be part of this project and I hope we will see the next steps of the industrial and research partners soon. In the meantime, I suggest keeping an eye on our website, we will be publishing the final CO2stCAP report soon.
Other articles you might be interested in
Get the latest CCS news and insights
Get essential news and updates from the CCS sector and the IEAGHG by email.
Can’t find what you are looking for?
Whatever you would like to know, our dedicated team of experts is here to help you. Just drop us an email and we will get back to you as soon as we can.
Contact Us NowOther articles you might be interested in
Get the latest CCS news and insights
Get essential news and updates from the CCS sector and the IEAGHG by email.
Can't find what you are looking for?
Whatever you would like to know, our dedicated team of experts is here to help you. Just drop us an email and we will get back to you as soon as we can.
Contact Us Now