
GHGT-17 Site Tour at Heidelberg Materials and Blindman Brewing
5 November 2024
Following the final day of GHGT-17, delegates embarked on four field trips, including a visit to Heidelberg Materials and Blindman Brewing.
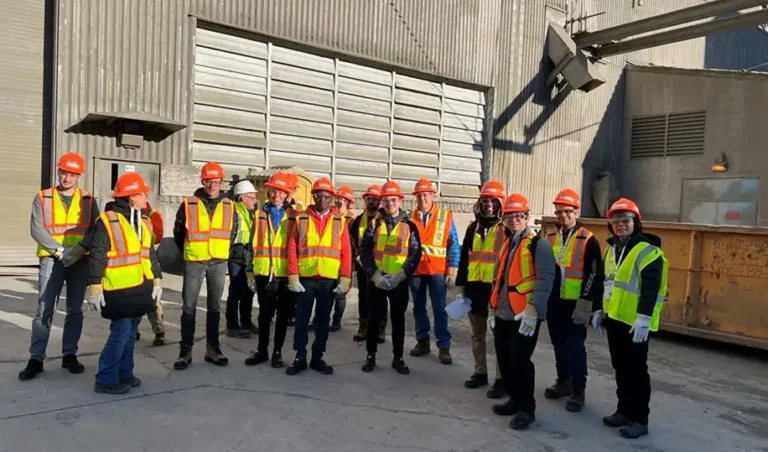
Following the final day of GHGT-17, delegates embarked on four field trips, including a site tour at Heidelberg Materials and Blindman Brewing.
Setting off early before sunrise on Friday, 26 October 2024, we travelled from Calgary to Edmonton for 180 minutes through Alberta’s sprawling prairies, witnessing the golden hues of sunrise stretching across the open plains as we made our way to Heidelberg Materials’ Edmonton cement facility and CCS pilot plants.
Site Tour at Heidelberg Materials
This site is preparing to host the world’s first full-scale carbon capture project on a cement plant, scheduled to be operational by late 2026, with the aim of capturing over 1 million tonnes of CO₂ annually from cement production and its combined heat and power facility. The site of the CO₂ capture plant is planned to be located 1.5 kilometers away and will receive flue gas transported from the cement facility.
Heidelberg Materials North America made progress on its carbon capture project by launching a two-stage competitive procurement process to select CO₂ capture technology and contractors. As part of this initiative, Technip Energies was awarded a front-end engineering and design (FEED) contract to deploy the Shell CANSOLV® CO₂ capture system[1], while MHI Low Carbon Solutions Canada, ULC. and Kiewit Energy Group Inc. were also awarded a FEED contract as a partner team to implement MHI’s Advanced KM CDR Process™ with the KS-21™ solvent[2]. During the site tour, a visit was made to the pilot plants testing both capture technologies: the Shell CANSOLV® system, with a capture capacity of 5 tonnes per day, and the MHI KS-21™, capable of capturing 0.3 tonnes of CO₂ daily. These pilot tests aim to assess how carbon capture technology can be integrated into an existing cement plant, confirm the impact of impurities, and refine the optimal design for a full-scale facility.
In addition to CCUS efforts, Heidelberg Materials is investing in the Alternative Low Carbon Fuels (ALCF) Project, which seeks to replace 50% of fossil fuels used in the kiln with low-carbon alternatives. This project involves building a 6000 m³ fuel storage facility and implementing systems to feed these alternative fuels into the calciner vessel, aiming to optimise combustion efficiency while reducing emissions.
The progress at Heidelberg Materials’ Edmonton site highlights a remarkable commitment to decarbonising cement production. Through innovative pilot testing and the integration of low-carbon fuels, Heidelberg is paving the way toward net-zero emissions in cement manufacturing. These pioneering efforts mark an important step forward for sustainability in heavy industry, setting a strong example for future applications of CCUS.
Blindman Brewing Tour
After wrapping up the site tour at Heidelberg Materials, the group set off on a 90-minute drive to Blindman Brewing in Lacombe, a central Alberta brewery known for implementing innovative carbon capture technology, which repurpose CO2 emissions directly into the brewing process. Along the way, we enjoyed a tasty lunch pack provided at Heidelberg, adding a nice touch to the journey.
In the brewing process, yeast consumes sugars and produces both alcohol and CO₂ as by-products. Traditionally, breweries must purchase additional CO₂ for carbonation, but the visit to Blindman Brewing highlighted their CO₂ capture and reuse system, which captures CO₂ from fermentation and reuses it to carbonate their beers sustainably. The compact, refrigerator-sized capture device, designed by Texas-based Earthly Labs and partially funded by Emissions Reduction Alberta (ERA), captures CO₂ at >99.9% purity, meeting beverage-grade quality standards[3]. The process includes three steps: gas is dried to remove moisture, scrubbed to eliminate volatile organic compounds (VOCs) and other impurities, and chilled to below -34.7 °C to convert the gas to a liquid.
By integrating this system, Blindman Brewing has reduced both carbon emissions and operating costs, CO₂ that would otherwise be purchased. This initiative not only advances sustainability in brewing but also serves as a valuable model. The Blindman Brewing is developing a dataset on emissions reduction and profitability to share insights with other breweries across Canada interested in adopting this environmentally friendly process.
At the end of the tour, delegates were treated to a beer tasting experience, sampling some of Blindman Brewing’s finest creations before heading back to Calgary just after sunset.
Reflections
This unique, two-part tour offered a fascinating look at the evolving role of CO₂ capture: from Heidelberg’s cement plant, a hard-to-abate industry where carbon capture is driving progress toward net zero, to the craft beer industry, where CO₂ is captured and reused in the brewing process.
Decades ago, CO₂ capture was initially used in gas sweetening, with the captured CO₂ later repurposed for enhanced oil recovery (EOR). Today, this technology is transforming industries in innovative ways.
[1] Carbon Capture Journal. Technip Energies awarded FEED for Edmonton CCUS project. February 2024.
[2] Carbon Capture Journal. MHI and Kiewit selected for Heidelberg Edmonton CCUS project. April 2024
[3] Chart. Small-Scale Carbon Capture. 2024
Other articles you might be interested in
Get the latest CCS news and insights
Get essential news and updates from the CCS sector and the IEAGHG by email.
Can't find what you are looking for?
Whatever you would like to know, our dedicated team of experts is here to help you. Just drop us an email and we will get back to you as soon as we can.
Contact Us Now