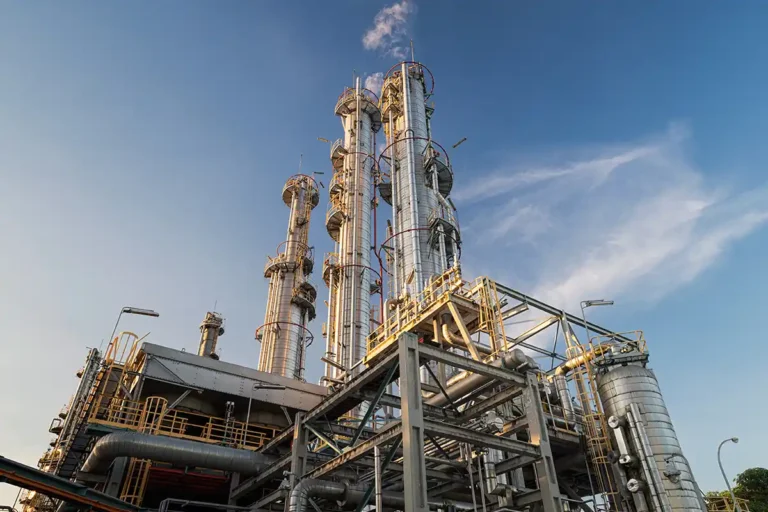
2023 Annual Experience Sharing Report for Northern Lights Phase 1 Facilities
22 May 2024
The report’s aim is to enhance future projects by offering insights and learnings in crucial areas such as project implementation, safety, efficiency, and sustainability.
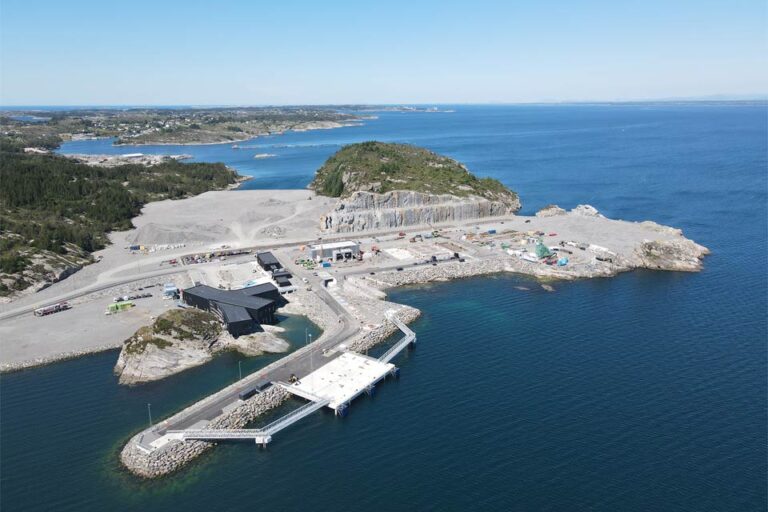
Introduction
As per their mandate, the Longship actors, Heidelberg Materials, Celsio Oslo Varme, and Northern Lights are charged with the dissemination of knowledge, experiences, and awareness of CO2 management. This commitment is fulfilled through detailed reports, facility tours, and engagement in conferences and presentations.
The Northern Lights experience report for the reception terminal and subsurface components (including pipes, well control, and geological storage) encompasses the period from 01 January 2023 to 31 December 2023. The aim is to enhance future projects by offering insights and learnings in crucial areas such as project implementation, safety, efficiency, and sustainability. The report distils knowledge and experiences into 10 thematic areas as provided below:
Quay Upgrade and Expansion
The civil design of the jetty on Northern Lights was performed approximately 2 years before detailed design of the ships, with jetty design in 2018/19 and jetty construction starting in the beginning of 2021. Consequently, the jetty design had to be based on preliminary assumptions of the final ship length and location of the central manifold as well as other key interface facilities.
Examination of the quay design uncovered mismatches between the initial calculations and the actual specifications required for docking ships, resulting in costly modifications. To prevent such issues in the future, it is stressed that quays should be designed with enhanced flexibility, allowing for adjustments in key ship design parameters. It is also recommended to include adequate margins in the design to accommodate uncertainties in ship specifications.
Flange Management
Corrosion and mechanical damage affected several ring-type joint (RTJ) carbon steel flanges, highlighting the necessity for enhanced personnel training and better upkeep of carbon steel pipe coils stored outdoors. It is advisable to adopt a more comprehensive flange management protocol that encompasses improved handling techniques and more rigorous maintenance standards.
Fixed Light Installations
The facility design incorporated a substantial number of fixed lights without considering that the facility is frequently unmanned, meaning that there will not be people present at the plant other than during offloading and maintenance activities. As CO2 is not flammable, it is also not subject to ATEX regulation[1]. This situation emphasizes the difficulty of incorporating project-specific needs into the design phase. To prevent future overruns, it is advisable to explicitly specify the requirements in the work scope outlined in the contract with the contractor.
Insulation Scope on Pipelines
While the insulation on piping at the Northern Lights plant was applied in compliance with specifications and requirements to avoid ice formation, it was overlooked that certain insulated pipe segments and valves would not be subject to icing during normal operations. This underscores the importance of improving evaluations and specifications to prevent superfluous insulation. A comprehensive assessment of insulation requirements is recommended to ensure its necessity.
Pipeline Cleaning with FCG
Flooding, cleaning, and gauging (FCG) is a routine process used for the maintenance and inspection of pipelines. Initially, the pipeline is filled with a fluid, typically water, to set the stage for cleaning. Following this, specialized equipment known as “pigs” is employed to scour the pipeline. Regular FCG is essential for preventing potential leaks and other issues that could lead to environmental damage or operational disruptions. Further, cleaning the CO2 pipeline to remove debris is vital, as debris can significantly reduce the injectivity of the well.
Despite six “pigs” being sent through the pipeline in June 2023, the pipeline was still deemed insufficiently clean, with more impurities present than expected. This highlights the necessity for meticulous planning in this area prior to CO2 injection. It is advised that multiple FCG cycles be conducted to ensure the pipeline meets cleanliness and safety standards.
Installation of DCFO and Nodes Using the ‘Lay-away’ Method
The Northern Lights Subsea Injection System (SIS) will be connected to the Oseberg A (OSA) platform[2] for operations. This connection is through the Direct Current Fibre Optic (DCFO)[3] cable and the umbilical. Northern Lights are amongst the first users of such a DCFO cable, meaning that there is no previous experience to build upon.
Lay-away is a technique employed during the installation of pipelines on the seabed. This approach involves initially laying the pipelines in a temporary position before they are shifted to their final location or before additional construction activities commence. The project initially adopted the ‘lay-away’ method. However, based on experience, the “lay-in” method is now recommended for future installations. This method involves methodically positioning pipelines directly at their designated seabed location where they will be permanently mounted.
Testing of DCFO Cable During Installation
The project initially implemented an installation sequence that involved testing each joint from both the Oseberg A (OSA) platform and the installation vessel. However, it was determined that conducting tests solely from the installation vessel would enhance operational efficiency, simplify the process, and reduce costs.
Review of the Start-Up Plan for Northern Lights
To get the Northern Lights facility up and running, a long list of activities must be performed both in parallel and consecutively. Some activities depend on other activities having been performed and others need to take place in the same areas, which means having a precise start-up plan describing these activities is crucial.
In September 2023, a comprehensive full-day workshop took place within the project, concentrating on essential activities leading up to and including the acceptance test (where the entire facility will be filled with CO2, including the pipeline and the injection of CO2 into the reservoir.). The outcome of the workshop was positive, leading to a recommendation for hosting similar events at least annually.
Specifications Suitable for the Purpose
Northern Lights is developed under a company specific management system and uses corporate specifications and guidelines established with the oil and gas industry as basis. These are not always fit for purpose as CO2 is not the same as hydrocarbons.
Time invested in developing solutions based on existing specifications has occasionally led to overdesign. This highlights the necessity for specifications that cater to cost-effective solutions across different products with substantially different risks. It is recommended to create a completely new set of specifications specifically tailored for CCS projects.
Application Process for CO2 Injection and Storage at Northern Lights
To inject and store CO2 at the Northern Lights facility, an application must be submitted to the Environment Directorate, adhering to pollution regulations. Once received, the Directorate forwards this application to the European Free Trade Association ((EFTA) Surveillance Authority (ESA)) for informational purposes. The Directorate then reviews the application and prepares a draft permit, which is sent to ESA for feedback. ESA has a four-month period to provide comments. The process involving ESA was a new requirement for those involved with Northern Lights, resulting in additional work. To improve efficiency, it is advised to adopt a streamlined approach by submitting a joint application for both injection and storage directly to the Environment Directorate and ESA.
Conclusion
The Northern Lights project not only progresses its own objectives but also contributes broadly to the CCS sector by emphasizing the critical role of continuous learning, adaptation, and rigorous evaluation. These efforts ensure that each step forward is informed by a deep understanding of both past outcomes and future potentials, aligning technical advancements with the overarching goals of environmental sustainability and operational excellence. This holistic approach is essential as we advance towards innovative solutions in CO2 management and strive to meet global sustainability targets.
For more detailed insights and information, the full report is available via the link provided HERE:
References
[1] European Commission. Equipment for potentially explosive atmospheres (ATEX)
[2] Equinor. The Oseberg Field Centre
[3] YouTube. DC/FO™ Direct Current Fibre Optic Cable Technology. 2022
Other articles you might be interested in
Get the latest CCS news and insights
Get essential news and updates from the CCS sector and the IEAGHG by email.
Can't find what you are looking for?
Whatever you would like to know, our dedicated team of experts is here to help you. Just drop us an email and we will get back to you as soon as we can.
Contact Us Now