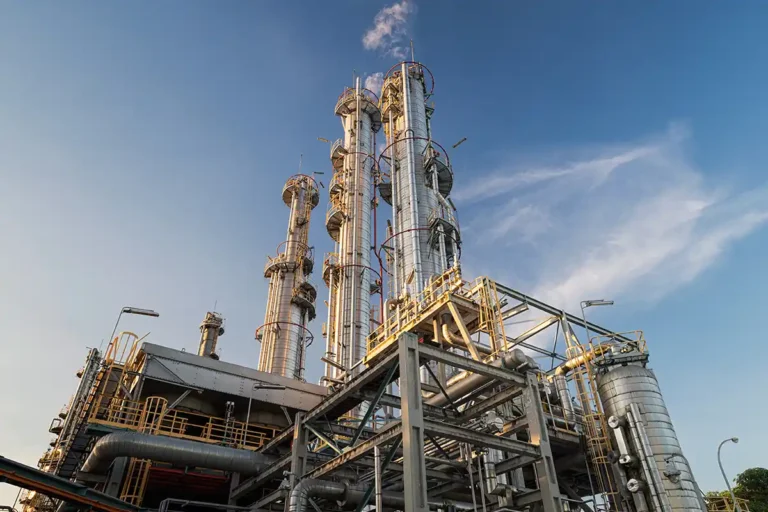
Low-Carbon Ammonia Roadmap (2023-03)
13 February 2023
This report examines the global ammonia industry today, low-carbon production options, infrastructure needs, potential uses for low-carbon ammonia.
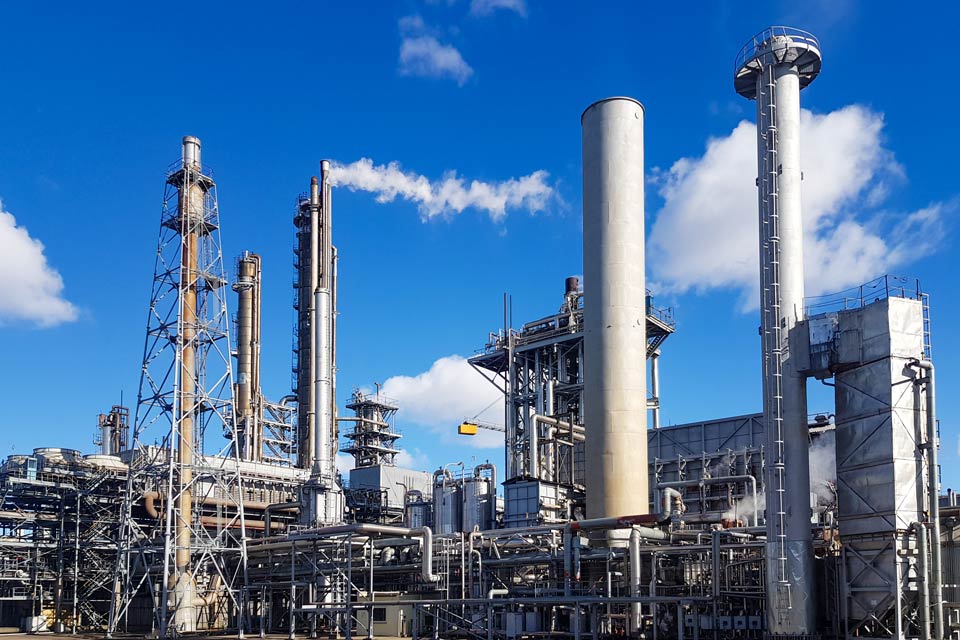
Background
Innovation for Cool Earth Forum (ICEF) published a report in November of 2022 titled ‘Low Carbon Ammonia Roadmap’ . This report examines the global ammonia industry today, low-carbon production options, infrastructure needs, potential uses for low-carbon ammonia, safety and local environmental issues, R&D needs, and policy options.
The development of the process to synthesize ammonia by German chemists, Fritz Haber and Carl Bosch has proven to be one of the most important technological advances of the 20th century. Half of the current global population could not be fed without synthetic ammonia. However, the flipside of this lifeline is that current methods of producing ammonia result in significant carbon dioxide (CO₂) emissions. Almost 2% of global CO₂ emissions come from the production of ammonia (responsible for 450 million tonnes (Mt) of direct CO₂ emissions , as well as an additional 170 Mt of CO₂e emissions due to the electricity consumed by the ammonia production process and release of nitrous oxide that occurs when ammonia-derived fertilizers are applied to agricultural land). Most of these emissions come from separating hydrogen from natural gas or coal.
Ammonia synthesis is significantly the largest CO₂ emitting chemical industry process (a ton of ammonia produced with the best available technology for SMR results in 1.8 tons of direct CO₂ emissions, with the possibility of reducing the emissions to 0.1 tons using CCS retrofits). Along with cement, steel, and ethylene production, it is one of the ‘big four’ industrial processes where a decarbonisation plan must be developed and implemented to meet the net zero carbon emissions target by 2050. These emissions could significantly be reduced with one or a combination of low-carbon production methods that include CCS, electrification, electrolytic and bio-hydrogen production.
The most expedient low-carbon ammonia pathway will vary by geography due to the importance of local resources and infrastructure and in due course some of the most promising pathways that are under R&D that are yet to mature for market.
The ammonia industry today
179 Mt of ammonia was produced in 2020 (250 Mt according to the IEA) from about 550 world’s fleet of ammonia plants, 72% via natural gas–based steam methane reforming (SMR), 26% from coal gasification, 1% from oil products and a fraction of a percentage via electrolysis. In terms of geographic concentration, China is the largest ammonia producer, at 30% of global production capacity, of which 85% relies on China’s coal reserves. The Middle East, United States, Russia, European Union, and India each account for 8–10%, with low-cost natural gas in the Middle East, Russia and the United States fuelling production.
State-of-the-art plants can produce natural gas-based ammonia at costs as low as $160/t due to economies of scale (typical capacities for new-build plants have progressively increased, from 2000 t/day in the 2000s and increasing to 3300 t/day today). However, this cost is significantly subject on the cost of feedstock natural gas, which contributes more than half of the levelized cost of ammonia production. As a result of notable rise in natural gas prices, world ammonia prices have increased dramatically since 2021, from $200–300/t to over $1000/t in Europe, the Middle East, and the United States. Idled capacity appears to be restarting in response to these price rises, but the market remains exceptionally volatile. High capital costs and plant lifetimes of 50 years builds impede the development of global ammonia production system. The capital investment (including engineering, procurement, and construction costs) for an SMR plant runs around $1.675 billion for the core equipment for 875 kt per year plant (would generate around 1 580 kt CO₂ per year) 4. A carbon capture and storage (CCS) retrofit would require capital investments of around $335 million, or about 20% of the initial investment cost. Modern SMR systems with a smaller primary reformer or oxygen-blown autothermal reformers (ATRs) is expected to potentially bring these costs down.
Degree of competitiveness for low carbon ammonia processes
The economic competitiveness of low carbon ammonia production processes will depend partly on the relative differences in their primary production cost drivers, e.g., cost of natural gas and clean electricity. The volatility of both natural gas and clean electricity prices creates an uncertain future production landscape. For example, from 2000 to 2020, market prices for ammonia ranged between $100/t to $600/t, but natural gas shortages starting in 2021 drove prices above $1000/t across the world (thus difficult to predict how expensive blue ammonia might become in the short term). As a result, green ammonia imports to Europe became cheaper than gray ammonia in 2022. This variation in energy prices over time and geography, in combination with the age and status of existing conventional ammonia production plants, leads to a complex scenario in which both blue and green ammonia facilities are being developed in different locations globally. While many analyses attempt to forecast the future balance between blue and green ammonia production, both need to be scaled to meet projections for growing future demand for low-carbon ammonia.
Another key factor in cost variation is the potential for different levels of centralization for blue and green ammonia production. Given that gray ammonia production is centralized, blue ammonia will likely be similar, resulting in additional costs for ammonia transportation and distribution of ammonia. This is estimated at $52/t via pipeline, $100/t via truck or $140/t via railway for 1600 km. The modularity of green ammonia production means there is less economic advantage from large-scale production facilities, creating greater opportunities for distributed production with lower transportation costs to end users.
A prime impediment for blue ammonia production is the supporting infrastructure to transport captured CO₂ to storage sites. Furthermore, while the concentrated process stream from reforming natural gas for blue ammonia is easily captured, capturing the dilute CO₂ from combustion is more difficult and expensive. For green ammonia, the primary obstacle for the deployment is its high cost. When assuming an electricity price of 7 cents per kWh, the baseline levelized cost for green ammonia is roughly $1000/t using renewable energy and $900/t using nuclear energy (In places where optimal renewable conditions produce low electricity prices, green ammonia may already be cost competitive, such as at prices of 4.5, 3.2 and 2.3 cents/kWh for utility solar in Morocco, Chile, and Saudi Arabia). The likely bottleneck for scale is the limited existing capacity to manufacture new electrolysers, leading to a discrepancy between announced projects and the likely ability to deliver on them. Green ammonia also struggles with the intermittency of renewable energy sources, potentially requiring the use of some higher-emissions grid-supplied. Further, all forms of low-carbon ammonia face the barrier of a market reluctance to pay a green premium for a lower carbon footprint, meaning they depend on policy to drive an uptake in demand and for subsidies to close the cost and corresponding price gap with gray ammonia.
Ammonia infrastructure
Utilizing ammonia as a fuel, feedstock or commodity requires special purpose infrastructure dedicated to trade, transportation, and fuelling. This infrastructure is independent of infrastructure for ammonia production (e.g., transmission power lines for green hydrogen production) or use (e.g., local fuelling infrastructure). The special purpose infrastructure includes pipelines for transportation, tanks for storage and facilities for maritime bunkering. The type of infrastructure needed is in general a function of the distance ammonia is being transported, with rail and maritime shipping commonly used for transporting ammonia long distances. At present, the limited extent of this infrastructure constrains the production, trade, shipment, monetization and use of ammonia. Inevitable chokepoints will slow ammonia deployment without substantial investment in permitting, siting, and building. The high capital costs and immature markets of today would benefit from new approaches to building and financing dedicated ammonia infrastructure.
Most ammonia ports today (120 ports out of 195 total) are receiving terminals linked to fertilizer production. Projected increases from announced projects would grow 50% by 2030 and 100% by 2040. Many of these will serve southeast Asia, for maritime fuelling and logistics support as well as local consumption and use.
For maritime fuel application, bunkering is a key prerequisite for deployment and requires separate consideration from fuel supply or cargo storage infrastructure. In many ports, physical space for these new elements (fuelling storage and bunkering facilities) is a limiting constraint. In others, fuel supply is the limiting constraint. For example, the storage tanks at bunkering facilities are commonly 25–50% greater capacity than the ships they serve.
There are over 270 US patents for ammonia storage technologies, almost all ammonia is stored in tanks (pressurized, low-temperature and semi-refrigerated systems). Costs are relatively well known and can represent a substantial cost to project developers. For a proposed Mt/y facility in Galveston, Texas, the two storage tanks required have a combined estimated cost of $500 million. Salt caverns could provide a storage option for large ammonia volumes at low cost. Salt caverns can store large amounts of energy indefinitely at low cost (~$1/kwH up-front cost).
Pipeline transport of liquid ammonia is a safe, low risk and, once installed, cost-effective mode of transporting ammonia between locations. Overall, ammonia pipelines appear to have an excellent safety record. The US does have several major trunk lines totalling nearly 5000 km, the US pipelines move over 2 million tons of ammonia per year (Mt/y) and were built with an estimated cost of ~$250 million in 2019 dollars.
New pipeline costs vary as a function of flowrate, length, diameter, geography, and temperature. Long-distance costs do not require compressors but do require pumps (usually centrifugal pumps). Costs are reasonably well understood, CAPEX costs are roughly $500/km/year and OPEX per booster station is ~$400,000/y.
In anticipation of ammonia infrastructure build out, recent research has focused on repurposing existing natural gas lines for ammonia transport. At ambient conditions (i.e., in gaseous form), the physical properties of ammonia and methane (such as density, specific heat, compressibility, viscosity) are quite similar. Based on limited study, there is no special metallurgy or retrofit required. However, the different chemistry of natural gas requires purging, decommissioning, and recommissioning prior to use for ammonia transport. Permitting bottlenecks and lack of human capital may limit the speed and scale to which natural gas systems could be converted for ammonia transport. In general, repurposing of existing infrastructure (natural gas, LPG, etc.) for ammonia transport is under investigated. This area represents another potential focus for R&D and analysis as part of a low-carbon ammonia.
Utilization of low-carbon ammonia
Approximately 70% of ammonia production globally is used to make fertilizers.4 While ammonia is used as a fertilizer because of its nitrogen carrier capability, it is now widely investigated for its hydrogen carrier capability. Typically, after ammonia decomposition, the hydrogen stream will be harvested and used for further applications, and the nitrogen stream will be directly vented to the atmosphere. This process requires energy input and results in inevitable energy loss, typically 0.28–0.30 MWh/ton-ammonia. For high purity hydrogen applications, 15% hydrogen loss is considered the current best practice scenario because only 85% of the input hydrogen can be recovered due to the purification process. The combination of energy and hydrogen loss leads to a total ammonia cracking efficiency of 76%. Additional losses will occur if there is a need for additional compression and transportation and delivery of the resulting hydrogen
Many of the proposed novel applications of low-carbon ammonia are based on combustion. However, these novel ammonia combustion applications all face similar challenges because of the drawbacks of combusting ammonia compared to well-established carbon-based fuels. Once ammonia or an ammonia-blend fuel has been ignited, maintaining flame stability is difficult because of the narrow flammability range in air. exhaust management of ammonia combustion is problematic because of the increased potential for ammonia slip and the formation of N2O and NOx. While the understanding of both pure and blended ammonia combustion has improved, pertinent knowledge gaps remain in the ability to fully model its physical and chemical properties in technologically relevant engines, turbines, and other systems.
Other applications discussed for ammonia in the ICEF report include marine fuel, power generation, heavy industry (feedstocks and energy source), heavy-duty road/surface transport, refrigerant/ coolant, and aviation fuel.
Conclusion
A synopsis of the findings from the ICEF report is provided below.
- The potential to replace fossil fuels with low-carbon ammonia at scale is not limited globally by natural resources or critical minerals (although local limits can be substantial).
- There are no technical barriers to producing low-carbon ammonia in large volume before 2030. Green hydrogen production faces manufacturing limits (for electrolysers) and siting constraints (for transmission and generation of zero-carbon electricity) that must be addressed to scale rapidly. Blue hydrogen supply is chiefly limited by CO₂ transport and storage access and can be accelerated by adding carbon capture to existing ammonia production units and new projects.
- Cost is the chief barrier to deployment. The use of low-carbon ammonia for fertilizer production would raise the cost of food and fibre production. When used as a fuel, low-carbon ammonia would cost substantially more than natural gas, coal, diesel or even hydrogen on an energy-density basis.
- Power-sector applications require advances in blending and feed systems, combustion science, ammonia fuel cells, environmental hazard management and improved efficiency of use.
Overall, there are significant challenges in extending the use of ammonia to new sectors. The most promising new uses are concentrated in shipping fuels and power generation. In both these sectors, significant growth in the use of ammonia is possible by 2030. In other sectors, new uses of ammonia are limited by technical challenges and competition from other low-carbon pathways, including electrification.
A near (1-3 years), medium (2-8 years) and long (4-15 years) term framework for low-carbon ammonia roadmap in production, application technology, transport & infrastructure, health & safety and policy has been provided in the ICEF report which can be accessed.
Other articles you might be interested in
Get the latest CCS news and insights
Get essential news and updates from the CCS sector and the IEAGHG by email.
Can't find what you are looking for?
Whatever you would like to know, our dedicated team of experts is here to help you. Just drop us an email and we will get back to you as soon as we can.
Contact Us Now